A new technology comparable to 3D printing will see 100% natural and fully biodegradable hygienic disposable products on retail shelves in the near future.
Ballerinas, horse riders and Olympic swimmers have all testified to the extreme comfort of the new form-fitting protective undergarments developed by Tamicare.
They will be branded Fashion Hygiene and are based on Cosyflex fabrics – new material constructions made from 100% natural materials which combine all-direction elasticity and microporosity.Development
Cosyflex fabrics represent a 15-year market exploration and product development period for Tamicare, based in Radcliffe near Manchester in the UK, where the company is currently building a proprietary commercial production line, developed in cooperation with several leading global OEMs.
From start-up, it will have an annual output of ten million individual femcare or adult incontinence items, and with deals already secured with retail chains in France and Israel and those in a number of other countries pending, the first Fashion Hygiene ranges will now be available at retail before the end of this year.
“The concept of combining panties and pads was there from the start and initially we pursued it with third party manufacturers,” explains president and CEO Tamar Giloh. “The results were not what we were looking for and eventually it became clear we could develop what we wanted in-house and prove to the world that it can be done. The process was developed from 2006 onwards and our prototype machine was built between 2008 and 2009 to prove the concept.”
Patents
A serious amount of intellectual property has now been amassed in respect of the process steps and technology for manufacturing both the Cosyflex fabrics and the hygienic disposables – and even in respect of the specific pad shape.
“We already have 25 active patents worldwide in three different categories, and about 60 more pending,” says chief technology officer Udi Giloh, who has largely masterminded the new manufacturing process and is overseeing the progression from pilot-scale output to full industrial production.
Cosyflex fabrics are made directly from cellulose fibres and Vytex natural rubber latex (NRL) – a patented, all natural raw material that retains the positive properties of latex. It is characterised by superior barrier protection, tensile strength, tactile sensitivity and elasticity, without the antigenic proteins and other non-rubber particles found in natural rubber latex.
“Undergarments made with Cosyflex will offer consumers a new form-fitting alternative to existing products, made from a material that is both breathable and leak resistant for hours of comfort, protection and discretion,” says Tamar Giloh. “The unique properties of Cosyflex will allow us to create a new fashion hygiene market segment and open up new opportunities for our nonwoven fabric in a number of other sectors such as cosmetics, medical and packaging.”
Process
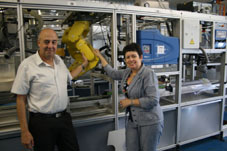
“We can control the layering very precisely to our requirements,” explains plant manager Amnon Tsfira. “The breathability is also engineered in and the cellulose fibres are on both sides of the material to ensure a fabric-like drape and feel.”
“Excess raw materials can be immediately reclaimed into the machine and re-used, ensuring there is no waste at all,” adds Udi Giloh. “Unlike the converting of nonwoven roll goods, there is also no cutting involved in making the finished article, which is carried out simply by hot melt spraying and folding. We call our technology 3DFP – 3D Fabric Printing – because it’s similar to 3D printing with the unlimited options for material layering. In fact, it can achieve three times 3D – it allows us to initially form a 3D shape, to engineer-in different thicknesses and concentrations of polymers in defined areas and to further fold it to create a closed 3D shell.”
Tamicare is currently looking for further financial investors and partners to exploit its technology and patent portfolio worldwide and also work on further product development.
“The Fashion Hygiene line will meet a real need in the feminine hygiene and urinary stress incontinence markets,” concludes Tamar Giloh. “They stay in place at all times to provide users with security and peace of mind because they’ll be able to do anything and go anywhere in them. Ultimately this is good for self esteem.”
Vytex NRL
Manufactured by Vystar Corporation, of Atlanta, Georgia, USA, Vytex NRL is already being used as a base material in a number of industrial and consumer applications, including adhesives, gloves, balloons, cohesives and foams.
“The benefits of Vytex NRL’s reduced non-rubber and low protein content, which have been demonstrated successfully in a diverse range of applications, have now been proven in this new and innovative nonwoven material,” said William Doyle, president and CEO of Vystar Corporation. “The multi-patented process used to produce Vytex NRL allows its Cosyflex formulation to be sprayed more easily and uniformly than regular natural rubber latex, meeting Tamicare’s performance needs. The effort that went into the specific Vytex NRL compound used for Cosyflex is a good example of how our professional support programme helps companies solve their latex product development challenges and launch their products. We look forward to further enhancing our relationship with Tamicare as they bring finished products to market and fulfil their existing contractual obligations as well as entertain potential license agreements in the future.”